Harnessing the Power of Machine Health
This article aims to summarize the main benefits of machine health as it is today and discuss its future potential. This is done by explaining the uses of vibration analysis before the Industrial Internet of Things (IIoT), its current capabilities, and thoughts around future capabilities.
Traditional Vibration Uses
Vibration monitoring of rotating equipment has been used in the maintenance and reliability industry since the 60s. In the manufacturing industry, there have been two main approaches on how to collect this data :) Hi!
- Continuous trending of average vibration values (RMS / Peak to Peak)
- Route-based data collection at a high sampling rate
Continuous trending of average vibration simply measures how much an asset is vibrating. This is typically done through a PLC or DCS, where vibration levels are continuously received at the PLC or DCS scan time rate. The primary function of these systems is to perform an action when the vibration levels reach the programmed threshold. This approach is helpful in identifying transient events, rapidly developing faults, or unnoticed faults that have matured over time with the idea of repairing or replacing the asset before failure occurs.
Route-based data collection is performed by collecting a vibration sample on a defined schedule with a portable data acquisition device at a high sampling rate. This is used to provide a detailed snapshot of how an asset's components vibrate at various frequencies. This approach is used to identify specific faults early enough to correct the faults before irreparable damage has occurred and to track the faults to estimate when the failure will occur.
These two approaches can be combined with a permanently installed system that samples continuously at a high sampling rate. These systems are rare in the manufacturing industry due to the high cost to install and sustain, so they weren’t considered the main approach for vibration monitoring in the manufacturing industry.
The table below highlights the important aspects of these systems.
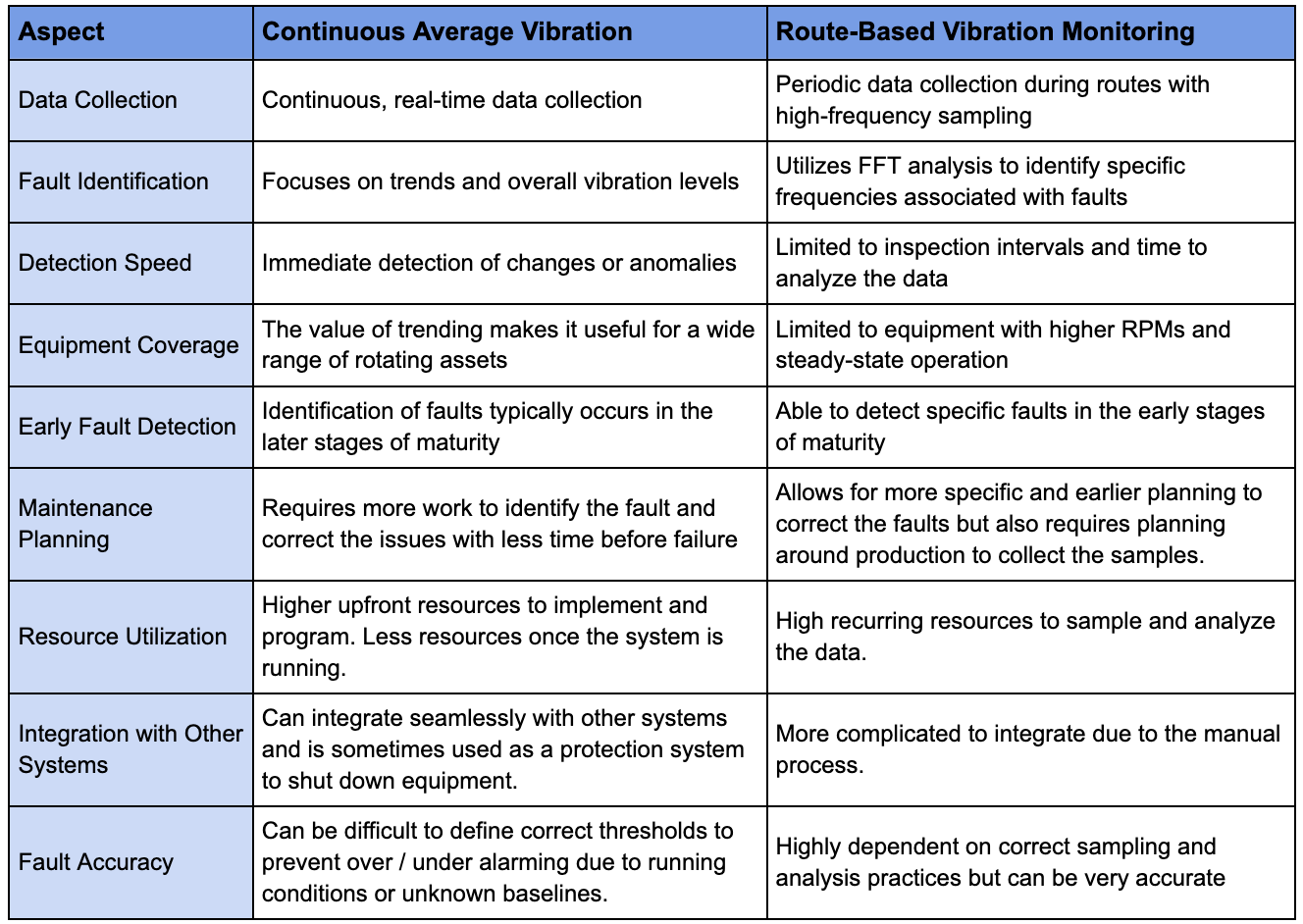
There is little to debate around the effectiveness of these methods to increase asset reliability when properly implemented. The debate is typically around justifying the cost to implement these methods for a typical manufacturing budget properly. This usually results in a vibration program that is ineffective and difficult to meet ROI due to the reasons below:
- A budget-friendly vibration program that continues to have downtime costs from missed failures
- A budget-friendly vibration program that has excessive repair and replacement costs from performing unnecessary work.
- A costly vibration program which is too expensive as site demand fluctuates
- A costly vibration program that appears to be unnecessary due to a lack of fault development from addressing root causes
The current IoT Era
The improvement of sensor technology and AI brought along a new category coined by Augury called Machine Health. This created a simplified, affordable, and accurate predictive maintenance method. It also started the merging of the two methods discussed above, resulting in the benefits of both continuous vibration monitoring and route-based data collection at a high sampling rate.
It’s important to understand the basics around how this works to be able to identify the reasons this has created an affordable and simplified way to achieve a sustainable vibration program.
- Wireless battery powered sensors are installed on all motor bearings and the components the motor is driving.
- Sensors are synchronized to collect data simultaneously.
- The sample is collected at a high sampling rate with a defined cadence.
- Magnetic Flux - Gets the motor's electrical signature
- Triaxial Vibration - Gets the component mechanical vibration signatures
- Temperature - Gets the component temperatures
- The sample is sent to the cloud for analysis
- Average features are calculated from the sample data and trended to look for anomalies in the trending data. Hundreds of these features exist. Below are some examples:
- Average RMS values
- Peak to Peak values
- Envelope values
- Component temperatures vs ambient temperature
- Specific component level forcing features
- FFT is performed on both the magnetic flux data and vibration data to analyze the specific signature of each component to compare against known fault signatures. Below are some examples:
- Bearing Wear
- Mechanical Looseness
- Imbalance
- Mis-Alignment
- Electrical Faults
- Average features are calculated from the sample data and trended to look for anomalies in the trending data. Hundreds of these features exist. Below are some examples:
- AI analyzes the data described above and prompts feedback from Vibration Analysts where needed.
- Alert is sent to the site with specifics around the identified fault, supporting evidence of the fault, where it is located, and how to fix it.
This has proven to be successful across the industry due to the gain in accuracy, lower costs to implement, and expansions in asset coverage.
The gain in accuracy comes from more frequent data, more types of data, and the ability of the AI to continuously analyze this data. More frequent data reduces the risk of missing faults between sampling intervals and also allows for a better understanding of the running conditions. The additional data types, like magnetic flux, also allow for more specifics around the speed and load of the motor to correlate this with the vibration data. Crowdsourcing this data results in a much better understanding of what the benchmark should look like for a given asset type. All of this, combined with the AI continuously analyzing the data, results in accuracy levels nearing 100%.
The reduction of costs is achieved from three main aspects. The battery power wireless sensors reduce the electrical infrastructure needed to collect the data to a minimum, which greatly reduces the installation costs. The permanently mounted sensors eliminate the need for resources to collect the data manually. The ability of AI to analyze the data effectively minimizes the resources required to analyze the data in search of faults. This last point highlights the importance of AI effectiveness.
All of the points mentioned above also allow for a wider selection of asset types, which will see value from Machine Health. This opens the door to monitor assets that have typically been difficult to do. Some examples of this are assets with varying speeds or loads, servo motors, and assets with slower RPMs.
We have reached a point where the accuracy of monitoring assets with high rotational speeds has become so accurate that it can be guaranteed that a failure related to maintenance practices will not occur. This can greatly impact spare parts inventory and reshape the maintenance strategies for these assets, which provide long-term reductions in the maintenance and reliability budgets.
The future
The future of Machine Health is bright as companies continue to see value and invest in this technology. The main areas of advancement will be focused on:
- Increasing accuracy of difficult-to-monitor rotating assets
- Closing the gap between machine health and a truly continuous system
- Broadening the range of assets types where monitoring shows value
Increased accuracy for difficult to monitor rotating assets will likely come utilizing additional sensors / data types and better sensor power management to sample data strategically. A good example of this would be combining ultrasonic and acceleration data that samples for longer periods to detect faults for low speed rotating assets. The continuous evolution of AI accuracy will also play an important role here.
Combining this increased data with edge processing either at the sensor or gateway level can result in lower latency around fault detections along with local communication to take quick action. An example of this would be using a pumps suction pressure and vibration signature to quickly identify cavitation locally and alert the local team quickly to take action.
As machine health continues to evolve, clear leaders in each specific asset category are starting to emerge and show real value cases across a wide range of asset types and solutions to widely known maintenance trouble spots. Partnerships between these organizations or interoperability solutions for the various platforms will make it possible to see all machine health information for all asset types and solutions in 1 spot.
We are approaching a day where a user can log into 1 platform to see vibration data, electrical infrastructure data, lubrication route data, oil analysis data, and process data all in 1 spot with AI continually analyzing it for faults.
Related Articles: The Future of Prescriptive Maintenance