Not really sharing insights but curious about implementation
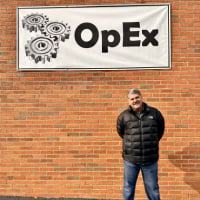
There is no question that Augury’s platform will deliver equipment insights that will result in significant equipment reliability improvements. However we all know that even the best systems can’t perform the final step to correct a problem by executing the fix. Augury’s platform will detect the defect, provide root cause and recommend a correction. All well and good. How do we ensure that the corrective action is executed by a human being at the plant? I call this the last yard. Just like an American football game, you can carry the ball all the way across the field but if can’t get it across the goal line it means nothing.
How do each of you ensure that the ball is carried across that goal line? How do you get a mechanic to take that recommendation and execute the fix? How does he/she cross that last yard and deliver the touchdown? I have returned to plants after a 5 year hiatus and the shop floor is very heavily taxed with issues and not enough resources to complete all required tasks. How do you make those corrective actions priority items?
Asking for a friend…😉
Comments
-
This is a challenge specifically with the level of turn over we have all experienced in the Maintenance Tech Field.
Our success was built around including Augury open and closed issues into the shift huddles and daily operations reviews (DOR) as a key KPI. These shift huddles (3-5 minutes reviews) and the DOR (15 Min) always included operators and Team leaders across the functions (production, quality, maintenance, etc). The key for us was to keep it visible and accountable. If the item was open, assign an owner and everyone knows who the owner is and what is the status of the open item. Owners can enter comment on status anytime.
We also incorporated these KPI's into our senior management reviews. Factory Weekly Operations Reviews (WOR) and the Monthly Operations Review (MOR) to ensure leadership had eyes on any trends related open and closed issues.
Finally, our final KPI inclusion was a monthly review within our executive leadership. Once again focusing trends across a group of plants, within a specific plant or specific process. If trending in a negative manner, an action was assigned to a executive to follow-up and seek resolution. Often this was a mere discussion with a specific factory to understand the reasons for a negative trend and what support was needed to correct the trend. Executive Owners would be responsible to report back on the action item in the next meeting which resulted in closure or further corporate support is needed. Staffing was one of biggest issues and working with Human Resources to focus recruitment often resulted.
Our key was to use the digital tool to create a high level of transparency across the organization. Since the data is always at our finger tips, there is not much effort to make it visible in the right format for each of these meeting formats. After that it is really leaderships responsibility to make sure there is accountability.
1 -
Sustaining the "fix" in many ways is the "holy grail" in operational excellence. The KPI's are an excellent means to understanding the course trajectory, but what is operationally available to ensure the fix sticks, it's context in terms of problem, indication/symptoms, source and solution are captured and preventive knowledge is disseminated? This requires the use of other tools (CMMS, AR/training, POKA) to ensure the problems and corrective actions are captured and translated for the future.
1 -
I like the analogy of the last yard 😃
To sustain the fix, I have seen as well that the use of KPIs is key and I would add that being this an important change to operate, the change management is also a critical. To align incentives, actions, rewards at the different plant and organization levels and to have the training and follow up required, especially with the actual turn over levels.
My two cents…
1 -
Great comments team! No question that you get what you inspect, focus on selecting the correct KPI is key as well as a process to track. Terry’s mention of shift huddles and daily review meetings are spot on. Use of nested management systems is key to supply chain effectiveness. Alvaro’s comments on thinking thru the change management process will ensure the initiative is successful by aligning the work with reward systems and support. Scott, I agree that to leverage the work it is necessary to think beyond the fix.
2