Back to the Future?
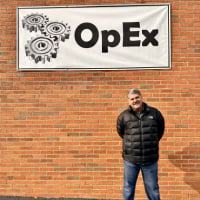
We spend a ton of time discussing innovation and cutting edge tech. It is exciting to learn about new ideas and concepts; new toys and shiny objects attract us. Many of the folks reading these posts are deeply technical which doesn't come without a super-charged dose of intellectual curiosity. We are the early adopters, enthralled by new capabilities and willing to suffer thru countless firmware updates and occasional bricking or dreaded screen of death.
But sometimes a look in the rear view mirror, a reboot of more basic, yet proven, manufacturing approaches yields opportunities. The two most impactful on my career as a young Ops leader were SPC and SMED.
Statistical Process Control (SPC) and its over arching philosophy of Total Quality Control (TQA) were the brainchildren of William Edwards Deming, an American business theorist and statistician. He developed a concept of optimizing factory output by reducing variability. Post WWII America was not interested in his concepts but Japan was. Fast forward and while Detroit was making horrible vehicles, Datsun, Toyota and Mitsubishi made huge inroads in American markets. All buoyed by Deming's quality approach. Not terribly difficult to learn and most of us may be able to dust off the cobwebs of college Stats courses once re exposed to the concepts.
The second technology is a bit younger but so relevant in today's world of SKU proliferation and customer and consumer customization. Today's consumer expects a product made to their tastes, specifications, package preferences, social causes etc. Today's customer wants company specific packaging and also exclusive LTOs! This creates an environment of short and frequent product runs. Package, flavor and brand changeovers are the norm and long runs of core products shrink. A nightmare for us efficiency minded folks. Why can't we make long runs of 4 pack toilet tissue or 12 pack beverage cans of one flavor? Pesky customers and consumers, that is why.
Single Minute Exchange of Dies (SMED) was developed by a Japanese Industrial Engineer that specialized in reducing changeovers from hours to minutes. His name was Shigeo Shingo and I was fortunate to meet him in person. I was responsible for bringing him from Japan to Chester, Pa. I was working for Scott Paper Co. and I had convinced leadership to contract with him to help us with package changeovers. He was very impactful. Years later I would use one of his practioners at PepsiCo to improve package changeover times significantly. I learned that repeatable beats fast every time. Get repeatable and then focus on speed. This is a whole course onto itself but so fruitful.
So here you go, two old fashioned, yet tried and true methods to improve your line output. That doesn't mean we don't embrace new technology but let us not forget proven, high impact and low cost methods either.
Back to the Future doesn't sound so bad does it? Maybe your flux capacitor needs a recharge!
Comments
-
Love it!
0